Fachbeitrag: Graphitstäube, zu soliden Blöcken gebunden, lassen sich als Sekundärgraphit in der Senkerosion einsetzen
Graphitelektroden für die Senkerosion bestehen aus isostatisch gepressten Graphitblöcken. Diese Graphitblöcke müssen vor der Verwendung zurechtgesägt werden, bevor anschließend die Geometrie eingefräst werden kann. Komplexe Geometrien können dazu führen, dass ein Großteil des Graphitblockes durch das Fräsen entfernt werden muss. Hierbei entsteht eine beachtliche Menge an Graphitstaub als Abfall. In einem Drittmittelprojekt wurde am Institute of Materials and Processes der Hochschule Karlsruhe an der Herstellung von Sekundärgraphit aus dem abgefrästen Graphitstaub geforscht.
Wassergläser als flüssiges Bindemittel
Um fein verteilte Stoffe wie Stäube miteinander zu verbinden, können flüssige Bindemittel verwendet werden. Soll aus Graphitstaub und Bindemittel ein Block aus Sekundärgraphit erzeugt werden, muss das Bindemittel eine Reihe an Anforderungen erfüllen. So müssen z. B. die elektrische Leitfähigkeit sowie die Beständigkeit gegen das Dielektrikum gegeben sein. Die größte technische Herausforderung liegt jedoch in den lokal auftretenden hohen Temperaturen, die durch das Wirkprinzip der thermischen Abtragung beim Erodieren auftreten.
Als potenziell geeignetes Bindemittel, welches die nötigen Eigenschaften aufweisen könnte, wurden Wassergläser ermittelt. Wassergläser setzen sich aus Siliziumdioxid und einem Alkalioxid zusammen, wobei das Alkalioxid ein Natrium-, Kalium- oder Lithiumoxid sein kann. Je nachdem welches Alkalioxid vorhanden ist, wird dann von Natronwasserglas, Kaliwasserglas oder Lithiumwasserglas gesprochen. Wassergläser werden meist in flüssiger Form verwendet und sind dann in Wasser gelöst. Eine wichtige Kenngröße für Wassergläser ist das molare Verhältnis. Dieses gibt das Verhältnis von Siliziumdioxid zu Alkalioxid an. Aus wirtschaftlichen Gründen wurde Lithiumwasserglas im Vorfeld ausgeschlossen, da die Kosten deutlich über denen für Natron- und Kaliwassergläsern liegen.
Mischen von Graphitstaub und Wassergläsern
Auf dem Weg zum soliden Block aus Sekundärgraphit müssen die flüssigen Wassergläser und der Graphitstaub zuerst miteinander vermischt werden. Wird Wasserglas zu Graphitstaub gegeben, so bilden sich zunächst zwei klar voneinander getrennte Phasen aus. Aufgrund der hydrophoben Eigenschaften von Graphit und dem Wasseranteil im flüssigen Wasserglas könnte der Einsatz von Benetzungs- und Dispergiermittel dementsprechend notwendig werden. Das Umrühren der voneinander getrennten Substanzen führt jedoch dazu, dass das Wasserglas völlig im Graphitstaub verschwindet. Dem trocken aussehenden Gemisch kann kaum angesehen werden, dass sich Flüssigkeitsanteile von bis zu 50 % in der Gesamtmasse befinden. Optisch ist das Gemisch daher nur schwer von reinem Graphitstaub zu unterscheiden.
Pressen und Aushärten
Das Gemisch aus Wasserglas und Graphitstaub wurde anschließend in eine Pressvorrichtung gefüllt und mit einer Drehdornpresse gepresst (siehe Abbildung 1). Große Anteile an Wasserglas sorgten für eine gute Verteilung des Bindemittels im Graphitstaub, führten jedoch auch zu einer klebrigen Masse, welche schwer oder nur unter Verlusten aus der Pressvorrichtung zu lösen war. Kleine Anteile an Wasserglas sorgten dafür, dass der Graphitstaub nicht vollständig von der Flüssigkeit benetzt wurde. Beim Auswerfen aus der Pressvorrichtung zeigte sich dies durch Teilausbrüche am erzeugten Block. Je nach verwendetem Wasserglas ergaben Massenanteile von 25 bis 40 % mechanisch stabile Blöcke.
Anschließend erfolgte die Aushärtung der Blöcke. Thermisch oder chemisch wird hierbei das Wasser aus dem Wasserglas ausgebracht. Bei der chemischen Aushärtung wurde Aluminium-Phosphat zum Gemisch zugeführt. Hauptsächlich wurden jedoch Versuche mit der thermischen Aushärtung durchgeführt. Bei Temperaturen von bis zu 350 °C wurden die Blöcke in einem Ofen temperiert. Das Temperieren erfolgte in Stufen, sodass sich der Block langsam aufheizen konnte. Die Aushärtung erfolgte meist nach dem Entfernen des Blockes aus der Pressvorrichtung (siehe Abbildung oben). Es wurden jedoch auch Versuche zur Temperierung unter Klemmkraft, welche durch eine Parallel-Schraubzwinge an der Pressvorrichtung aufgebracht wurde, durchgeführt.
Die größte Herausforderung bei der Aushärtung war die teilweise massive Rissbildung, die durch das Verdampfen des Wassers entstand. Die so erzeugten Blöcke waren dadurch sehr brüchig und konnten nicht weiterverwendet werden. Verschiedenste Benetzungs- und Dispergiermittel sorgten dafür, dass die Ausbrüche beim Pressen und die Rissbildung bei der Aushärtung deutlich zurückgingen. Jedoch zeigte sich, dass die Festigkeit der Blöcke bei fast allen Versuchsreihen mit Benetzungs- und Dispergiermittel abnahm. Wahrscheinlich haben alle getesteten Benetzungs- und Dispergiermittel die Wassergläser negativ beeinflusst. Ein geringer Teil der verschiedenen Rezepturen erzeugte jedoch Blöcke aus Sekundärgraphit, welche sich für eine Weiterverarbeitung eigneten.
Fräsen und Erodieren
Durch die runde Pressvorrichtung wurden zylindrische Blöcke erzeugt, die teilweise auch Ausbrüche vorwiesen. Damit für das anschließende Erodieren jedoch die gleiche Geometrie für alle Blöcke verwendet werden konnte, wurden die Blöcke plangefräst (siehe Abbildung 3).
Rezepturen, welche bis hierhin Erfolge erzielen konnten, mussten während des Fräsens aussortiert werden. Einige Blöcke hielten der Druckbelastung beim Einspannen in den Elektrodenhalter einfach nicht stand, andere Blöcke wiesen unter der Oberfläche Nester von nicht verklebten Graphitpartikeln auf.
Nachfolgend wurden die plangefrästen Blöcke dann in der Senkerosion getestet. Die plangefräste Fläche wurde zur Hälfte über dem Werkstück positioniert und eingesetzt. Dadurch konnte nach dem Erodieren der Verschleiß durch das Erodieren direkt mit der unbenutzten Teilfläche verglichen werden.
Vorgehensweise für das beste Ergebnis
Ein vollständiges Erodieren war mit keinem der Blöcke aus Sekundärgraphit möglich. Jedoch konnten Blöcke mit Natronwasserglas als Bindemittel erste vielversprechende Ergebnisse erzielen und die Werkstückoberfläche An-Erodieren. Das beste Ergebnis erzielte ein Block aus Natronwasserglas mit einem großen Anteil Siliziumdioxid bei ca. einem Drittel Massenanteil des Wasserglases und zwei Drittel Massenanteil für Graphitstaub.
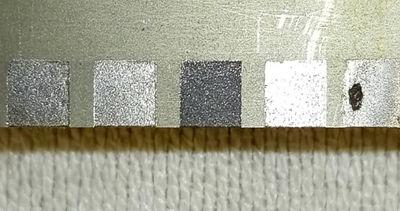
Abb. 4: Ergebnisse aus dem Erodieren bei verschiedenen Einstellungen; ganz rechts: Einbrand durch Lichtbogenbildung
Der Graphitstaub wurde bei einem Siebschnitt von 50 µm im Vorfeld klassiert, um ihn von groben Partikeln zu befreien. Anschließend wurde er in einem Becherglas vorgelegt und eine Mulde im Haufwerk erzeugt, in welche das Natronwasserglas pipettiert wurde. Vermischt wurden die beiden Substanzen mit einem Rührspatel. Danach wurde das Gemisch in die Pressvorrichtung gegeben und händisch in der Drehdornpresse gepresst. Die erste Aushärtung erfolgte mithilfe von Parallel-Schraubzwingen, um den Druck aufrecht zu halten, und verlief über zwei Stunden bei 100 °C. Für die zweite Aushärtung wurde der Block aus der Pressvorrichtung genommen und nochmals lose bei 230 °C für weitere zwei Stunden ausgehärtet. Durch die Verwendung eines Trennmittels konnte ein Ankleben der Masse in der Pressvorrichtung weitgehend verhindert werden.
Beim Fräsen wurden keine besonderen Einstellungen verwendet. Es wurde lediglich ein sehr niedriger Vorschub gewählt, um die mechanische Belastung zu minimieren. Für das Erodieren wurden Einstellungen im Bereich des Vor- und Feinschlichten gewählt und verschiedene Entladeenergien und Leerlaufspannungen getestet. Nennenswerte Unterschiede konnten durch die verschiedenen Einstellungen jedoch nicht erzielt werden. Gelegentlich kam es zu Lichtbogenbildung und den dementsprechenden Oberflächenschädigungen in Form von Einbränden an Werkstück oder der Elektrode aus Sekundärgraphit (siehe Abbildung 4).
Potenzielle Verbesserungsansätze werden bei der Gestaltung des Pressprozesses vermutet, zum Beispiel indem isostatisches Pressen eingesetzt wird. Hierdurch könnten dichtere Blöcke erzeugt werden und es zu einer besseren Verteilung des Wasserglases kommen. Auch die Suche nach einem Benetzungsmittel mit weniger Einfluss auf die Bindekraft des Wasserglases könnte zu besseren Ergebnissen führen.
(EU-Recycling 02/2022, Seite 33, Autor/Fotos: Stefan Pogontke, M. Sc. Verfahrenstechnik, Hochschule Karlsruhe – Technik und Wirtschaft)