Herbold-Waschanlage rückt PP-Hartkunststoff zu Leibe
Für die Primärproduktion von einer Tonne Polypropylen – der weltweit am zweithäufigsten verwendete Kunststoff – werden rund 5,2 Tonnen Rohstoffe benötigt und 1,7 Tonnen Treibhausgase freigesetzt. Wohingegen bei der Nutzung von einer Tonne Polypropylen aus Sekundärrohstoffen, etwa aus Kunststoffabfällen, nur um die 225 Kilogramm Ressourcenverbrauch und eine knappe Tonne Treibhausgase anfallen.
Von der Tatsache einmal ganz abgesehen, dass Kunststoffe, die nicht ordnungsgemäß entsorgt werden, eine immer größere Belastung für unsere Umwelt sind – und seit Jahren im Umfang von etwa zehn Millionen Tonnen jährlich in den Weltmeeren landen. An Recycling führt von daher kein Weg vorbei.
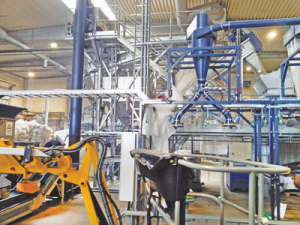
Doppel-Bigbag-Station für PP-Flakes und herausgesichtetes Leichtgut (im
Vordergrund) (Foto: Herbold Meckesheim)
Hoher Reinheitsgrad der Rezyklate
Herbold Meckesheim hat eine neue Waschanlage zur Zerkleinerung und Reinigung von Hartkunststoffen aus Polypropylen im Programm, die sehr erfolgreich im Einsatz ist, um Regranulate zu erzeugen. Gelobt werden sowohl der hohe Reinheitsgrad der Rezyklate als auch der große Durchsatz, dazu die Belastbarkeit und Wartungsfreundlichkeit sowie der hohe Automationsgrad. Ausgelegt für hohe Kapazitäten und für einen 24-Stunden-Dauerbetrieb, lassen sich zwei Tonnen PP-Flakes in der Stunde produzieren – bei einer Restfeuchte von weniger als einem Prozent und einer Flake-Größe von kleiner-gleich zwölf Millimetern.
Wie sieht eine Beispielanlage im Detail aus? Zunächst rieselt an einer Bigbag-Entleerstation das PP-Shredder-Gut über den Bodenauslauf des Bigbags in einen Trichter mit 0,5 Kubikmetern Volumen. Von hier wird das Material via Schnecke auf ein Förderband ausgetragen. Ein großer Pufferbunker (Typ SB2) von rund zwei Kubikmetern führt den Materialstrom gleichmäßig dem nachgeschalteten Störstoffabscheider zu. Was etwa bei einem direkt vorgeschalteten Shredder mit seiner ungleichmäßigen Abgabe wichtig ist.
Leistungsstarke Nassschneidmühle
Der zuverlässige Störstoffabscheider (Typ SAS 50/430) sondert schwere Fremdstoffe wie Metalle, Steine oder Glas ab, zum Schutz der nachgeschalteten Einheiten wie Schneidmühle und Friktionswäscher. Um Verluste an Polypropylen zu minimieren, ist eine Aufströmung durch eine Pumpe integriert. Die leistungsstarke Nassschneidmühle (Typ SML 60/145) übernimmt dann die Zerkleinerung der auf 30 Millimeter vorgeschredderten PP-Flaschen. Durch eine hohe Friktion erzielt die Mühle einen ausgezeichneten Reinigungseffekt und weist durch die Wasserzugabe einen geringen Verschleiß an Schneidmessern, Gehäuse und Sieb auf. Der Rotor besitzt austauschbare Messerauflagen und die Verschleißplatten sind auswechselbar, wodurch die Maschine kombiniert mit der optimalen Zugänglichkeit komplett verschleißgeschützt ist.
Im nächsten Schritt reinigt der Friktionswäscher (Typ FA 3000) die PP-Flakes intensiv. Dabei scheidet er Schmutzwasser genauso wie Feinanteile und Papierfasern ab und fördert das Produkt weiter zum Trenntank; der Rotor des Wäschers ist dank auswechselbarer Verschleißplatten wartungsarm. Im Trenntank (Typ SSB 4000/1800) – mit Wasser als Medium zur Dichtetrennung – werden die Flakes als Schwimmgut mithilfe einer Entwässerungsschnecke zum nachgeschalteten mechanischen Trockner transportiert und Partikel mit einer Dichte von über einem Gramm pro Kubikzentimeter wie PVC oder PET als Sinkgut von einem Kratzkettenförderer ausgetragen.
Geringer Reinigungsaufwand
Der mechanische Trockner (Typ T 1015 PA) befreit die gewaschenen PP-Flakes von Feuchtigkeit und scheidet Restverschmutzungen wie Papierfasern ab. Eingebettet in ein feuerverzinktes Gehäuse, bietet die Maschine eine pneumatisch betätigte, mechanische Abreinigung mit Spülvorrichtung für die Sieboberfläche und auswechselbare Verschleißplatten an den Rotorflügeln für geringen Reinigungsaufwand. Über eine ebenfalls pneumatische Förderung folgt der Weitertransport zum Windsichter (Typ SZS 630/212), der mit einem Kanal in Zick-Zack-Bauweise zum Heraussichten von Leichtgut wie Folien, Textilien, Fasern oder Staub aufwartet.
Zur Absackung steht schließlich eine Doppel-Bigbag-Station bereit. Hier werden die beiden Produkte Leichtgut und gereinigte PP-Flakes pneumatisch in Bigbags abgepackt. Die gesamte Anlage lässt sich bequem mit Comfort-Touch-Panel automatisch steuern (Siemens S7-1500). Schwankungen im Material werden zudem durch eine gezielte Regelung der Anlagenkomponenten ausgeglichen, was für eine maximale Leistungsausbeute sorgt. Dank der intelligenten und automatisierten Steuerung ist ein effizienter Betrieb mit geringem Personaleinsatz gewährleistet.
(Erschienen im EU-Recycling Magazin 07/2022, Seite 40, Foto: Herbold Meckesheim)