PEF-Bausteine aus Zellulose
Nachwuchsforscher am Rostocker Leibniz-Institut für Katalyse (LIKAT) entwickelten ein katalytisches Verfahren für Biopolymere. Ergebnis sind Bausteine des Kunststoffs Polyethylenfuranoat (PEF), die eine nachhaltige Alternative zu Getränkeverpackungen aus PET darstellen.
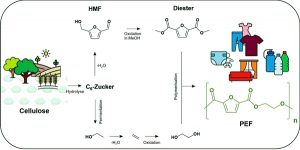
Auf Basis von Cellulose kann mit geeigneten Katalysatoren in wenigen Schritten ein nachhaltiger Kunststoff hergestellt werden. Die Anwendungszwecke des PEF sind vielseitig: von Textilfasern über Windeln bis hin zu Verpackungsmaterialien (Grafik: LIKAT)
Die Herstellung der PEF-Bausteine kommt ohne Erdöl aus; benötigt wird stattdessen Zellulose, also Biomasse, und im Wesentlichen nur noch Alkohol und Luft. Wie Projektleiter Dr. Esteban Meija erläutert, kommt das Verfahren mit maximal 60 Grad Celsius aus, funktioniert bei normalem atmosphärischen Druck und kann seine Produktivität unter kontinuierlichen Flussbedingungen um das 15-fache steigern.
Plattformchemikalie aus Reisstroh
Ausgangsstoff für die PEF-Bausteine ist eine sogenannte Plattformchemikalie, ein Furan-Derivat namens Hydroxymethylfurfural (HMF), das aus Zellulose, einem Mehrfachzucker aus Abfällen etwa der Landwirtschaft, produziert wird. Weltweit forschen Labors an insgesamt einem Dutzend solcher Plattformchemikalien, um die Rohstoffbasis der Chemie im großen Maßstab von Erdöl und Erdgas auf Biomasse umzustellen. Zusammen mit der Technischen Universität Hanoi wurde ein vereinfachtes Verfahren für die Herstellung von HMF aus Reisstroh entwickelt.
Luftballons im Labor
Prinzipiell reagiert bei diesem Verfahren ein Gemisch aus HMF und Alkohol mit Sauerstoff und unter Beisein eines Katalysators zu einem Ester, genauer gesagt einem Diester, der in einem weiteren Schritt zu PEF polymerisiert werden kann. Verglichen mit dem bisherigen Verfahren kommt das neue Verfahren mit einem Bruchteil an Wärme und Druck aus. Obendrein führen die Forscher den benötigten Sauerstoff nicht in konzentrierter Form zu, sondern aus der Luft – was den Prozess wesentlich vereinfacht. „Anfangs nahmen wir einfach Luftballons, bliesen sie im Labor auf und stülpten sie über die Apparatur“, erzählt Meija.
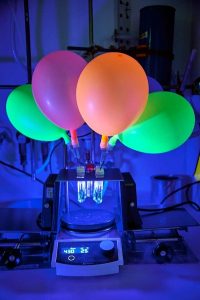
Experiment mit Gaseintrag ins Reaktionsgefäß: „Anfangs nahmen wir einfach Luftballons, bliesen sie im Labor auf und stülpten sie über die Apparatur“ (Foto: Nordlicht/LIKAT)
Die Verwendung von Raumluft hatte für die Reaktion allerdings einen Nachteil: Sie lief zu langsam. Das Produkt ließ sich erst am nächsten Morgen begutachten. Meija und sein Team lösten das Problem an zwei Stellen. Zum einen erhöhten sie leicht den Druck und fanden ein Optimum bei 20 bar. Zum anderen ersetzten sie das Reaktionsgefäß durch einen Microflow-Reaktor.
Kontinuierlicher Prozess
Dabei werden die Ausgangsstoffe, im Wesentlichen ein Mix aus HMF und Alkohol, mit Sauerstoff oder Luft durch ein System von feinen Röhrchen gepresst. Durch die kapillare Zwangsführung kommen die Sauerstoff-Moleküle gewissermaßen wohldosiert mit dem Ausgangsmix in Kontakt. Danach passiert das Reaktionsgemisch eine Kartusche. Dort befindet sich der Katalysator, der die Reaktion auf Trab bringt, in diesem Fall Partikel aus Kobaltoxid und Ruthenium, aufgebracht auf die Oberfläche kleiner Kügelchen.
Diese Anordnung sorgt für die „oxidative Veresterung“, wie Chemiker diese Reaktion nennen, und vor allem ermöglicht sie einen kontinuierlichen Prozess. Der Katalysator wird nicht verbraucht; er kann immer wieder verwendet werden. Das Produkt, der veresterte PEF-Baustein, verlässt die Kartusche als Flüssigkeit und kann nun polymerisiert werden.
(EU-Recycling 08/2020, Seite 23, Grafik: LIKAT)