Pöppelmann auf den digitalen Fachpressetagen 2020: Kreislaufkonzepte für die Automobilindustrie
Die Pöppelmann Gruppe setzt auf Eco-Design, um Produkte zu entwickeln, die ökonomische und ökologische Aspekte in Einklang bringen und Kunden einen größtmöglichen Mehrwert bieten. Innovative Projekte belegen, dass dies auch für streng regulierte Branchen wie die Automobilindustrie möglich ist. Auf den digitalen Fachpressetagen der Agentur Köhler + Partner am 5. November stellte Matthias Lesch, Geschäftsführer bei der Pöppelmann GmbH & Co. KG, das Konzept des Unternehmens vor.
Drei Ansätze – Reduce, Reuse und Recycle – bilden den Rahmen für die verantwortungsvolle Produktentwicklung. „Reduce“ bedeutet, den Materialeinsatz durch ressourcenschonende Artikelkonzepte und effiziente Produktionsverfahren zu reduzieren. „Reuse“ beinhaltet, an der Entwicklung von Produkten zu arbeiten, die für eine mehrfache Verwendung gedacht sind. Und unter dem Stichwort „Recycle“ erarbeitet der Kunststoffspezialist zukunftsweisende Konzepte, um Wertstoffkreisläufe zu schließen.
Hierfür wurde die unternehmensweite Initiative „Pöppelmann blue“ ins Leben gerufen, die alle Aktivitäten der Gruppe bündelt, die einen geschlossenen Materialkreislauf forcieren. Und das Unternehmen kann bereits eine Reihe von erfolgreichen Projekten präsentieren, die für Circular Economy stehen: von vollständig recycelbaren und zirkulären Pflanztöpfen des Geschäftsbereichs Teku aus Post-Consumer-Recycling-Material aus den dualen Systemen über PCR-Schutzkappen und -stopfen der Division Kapsto bis hin zu Non-Food-Universalverpackungen der Sparte Famac aus 100 Prozent PCR im eingesetzten Kunststoff.
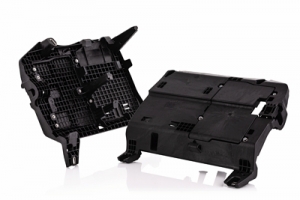
Die Division K-Tech
demonstriert am Beispiel „Halter SAM“, wie sich Leichtbau, Funktionsintegration und Ressourcenschonung vereinen lassen (Foto: Pöppelmann)
Die Division K-Tech
Die Division Pöppelmann K-Tech hat sich auf die Entwicklung und Serienproduktion hochpräziser technischer Kunststofflösungen spezialisiert und realisiert bereits verschiedene Ansätze für Kunden aus der Automobilbranche. Im Geschäftsbereich werden bereits etwa 20 Prozent des gesamten Materialverbrauches durch Rezyklate z.B. PP GF30, PP T20, PA6/PA66 GF 30, PC oder ABS abgedeckt. Die eingesetzten Rezyklate stammen aus Rückführungen von Angüssen aus eigenen Produktionsressourcen, externen Zukäufen und aus der hauseigenen Compoundierung.
Bis zum Jahr 2025 soll die Rezyklatquote im Geschäftsbereich K-Tech 35 Prozent der gesamten Materialeinsatzmenge erreichen. Um den Kunden höchste Verlässlichkeit zu gewährleisten, führte Pöppelmann verschiedene Grundlagenuntersuchungen durch, stellt Materialdatenblätter für Rezyklate bereit und bietet die Möglichkeit der Durchführung von FEM-Berechnungen, also den Nachweis der Bauteilfunktion, für den Einsatz von Rezyklaten.
Bei der Nutzung von Rezyklaten wird Wert auf eine klare Differenzierung von Post-Industrial-Rezyklat (PIR) und Post-Consumer-Rezyklat (PCR) gelegt. PCR-Materialien sind möglichst vorzuziehen. Bei PIR handelt es sich um recycelte Produktionsabfälle wie Angüsse und Produktmaterialien, die noch nicht im Einsatz waren. PCR wird hingegen durch die Wiederverwertung des Materials eines Produkts nach dessen Nutzung gewonnen.
Ein anderes Verfahren
Auch ressourcenschonende Produktionsverfahren kommen bei der Pöppelmann Gruppe zum Einsatz. So bietet der Thermoplastische Schaumspritzguss (TSG) im Vergleich zum Kompaktspritzguss ein erhebliches Einsparungspotenzial, bezogen auf das Material und das Gewicht des fertigen Bauteils. Der Kunststoffspezialist setzt hier unter anderem das MuCell-Verfahren ein.
Bei diesem physikalischen Schäumverfahren werden durch das Einbringen von Treibmittel direkt in die Kunststoffschmelze mikrozellulare Strukturen gebildet. Das macht ein Kunststoff-Bauteil nicht nur sparsamer im Materialeinsatz und deutlich leichter im Gewicht, sondern hat auch funktionelle Vorteile: Die physikalisch geschäumten Formteile weisen eine verbesserte Dimensionsstabilität auf, denn das injizierte Gas sorgt dafür, dass sich das Bauteil kaum verzieht. Pöppelmann K-Tech hat die Kennwerte für die MuCell-Materialien (TSG) im geschäumten Zustand festgelegt und produziert bereits diverse Serienbauteile für namhafte Hersteller im TSG-Verfahren, zum Beispiel Batterieboxen, Halter und Bodenplatten.
Einsparungen von bis zu 70 Prozent
Eine Modellrechnung von Pöppelmann K-Tech zeigt, dass sich mit der Kombination verschiedener Ansätze zu Ressourcenschonung im Automotive-Bereich bis zu 70 Prozent Material einsparen lässt: Eine optimierte Konstruktion vermeidet zehn bis 30 Prozent, zum Beispiel durch Wandstärkenreduzierung oder Rippenminimierung. Der Wechsel zu einem anderen Material von geringerer Dichte (z. B. von PA GF zu PP GF) spart bis zu 25 Prozent ein. Durch den Einsatz eines technischen Schäumverfahrens wie MuCell (TSG) lassen sich noch einmal drei bis 15 Prozent reduzieren.
Aktuelle Entwicklungsschritte und Pilottests
Die Division Pöppelmann Kapsto, die ihre Schutzelemente aus Kunststoff unter anderem an die Automobilindustrie liefert, erprobt aktuell mit einem namhaften OEM eine Rückführung der temporären Schutzabdeckungen für Abgaskrümmer und Gehäuse statt einer Entsorgung nach Verwendung. Die Artikel werden nach Nutzung in der Produktion durch Pöppelmann abgeholt, gemahlen und von einem Partner granuliert. Das Material steht dann zur Herstellung neuer Schutzelemente bereit.
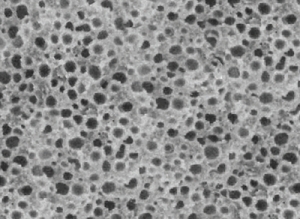
Thermoplastischer Schaumspritzguss (TSG) ersetzt für Kunden aus dem Automotive-Bereich oft den Kompaktspritzguss (Foto: Pöppelmann)
Die Division K-Tech erprobt aktuell die Nutzung von Material, das aus Verpackungsabfällen aus den dualen Systemen gewonnen wird – zur Produktion von Kunststoffartikeln für die Automobilbranche. PCR-Materialien auf Basis reiner Polypropylene wurden bereits gereinigt und mit 30 Prozent Glasfaser granuliert. Auch Bemusterungen zur Ermittlung von Kennwerten in Kompaktspritzguss und TSG wurden erstellt und auf Basis der Bauteilanforderungen und der Geruchs- und Emissionsanforderungen die geeigneten Bauteile ausgewählt und geprüft. Ein konkretes Projekt mit einem namhaften OEM ist in der Bemusterungsphase und soll 2021 in Serie gehen. Und die Entwicklung geht weiter: In Zukunft will Pöppelmann K-Tech auch Sichtteile aus PCR für den Fahrzeuginnenraum herstellen.
(Erschienen im EU-Recycling Magazin 12/2020, Seite 26, Foto: Pöppelmann)